7 Dicas Essenciais para Conserto de Máquinas Industriais
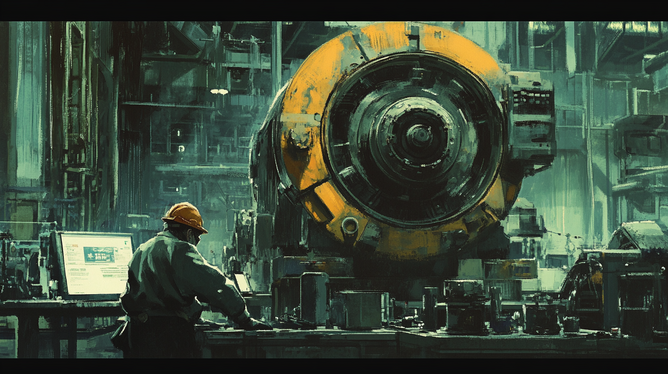
Por: Fabrício - 27 de Setembro de 2024
O conserto de máquinas industriais é essencial para garantir a continuidade e eficiência da produção. Neste artigo, vamos explorar as melhores práticas para realizar esse conserto com sucesso. Você aprenderá sobre manutenção preventiva, diagnóstico de problemas comuns, escolha das ferramentas certas e quando é hora de chamar um profissional especializado. Continue lendo para manter suas máquinas em perfeito funcionamento e evitar paradas inesperadas.
Manutenção Preventiva: O Segredo para Evitar Paradas
A importância da manutenção preventiva no Montagem de painéis elétricos industriais e outros componentes de máquinas industriais não pode ser subestimada. Esse tipo de manutenção é essencial para garantir que os equipamentos funcionem de forma eficiente, minimizando o risco de falhas inesperadas que podem paralisar a produção.
Uma manutenção preventiva bem planejada inclui a inspeção regular de todos os componentes da máquina, desde pequenas peças até sistemas complexos. A substituição de peças desgastadas antes que elas apresentem problemas pode evitar danos maiores e custos elevados com reparos de emergência.
Além disso, a manutenção preventiva também ajuda a prolongar a vida útil das máquinas industriais. Quando os equipamentos são mantidos em boas condições, eles tendem a operar de maneira mais eficiente por mais tempo. Isso não só reduz os custos com a substituição de máquinas, mas também aumenta a confiabilidade da operação, uma vez que paradas inesperadas são menos prováveis.
Outro benefício significativo da manutenção preventiva é a melhoria da segurança no ambiente de trabalho. Máquinas em mau estado de conservação podem representar riscos para os operadores, como a possibilidade de acidentes devido a falhas mecânicas ou elétricas. A manutenção regular ajuda a identificar e corrigir esses problemas antes que eles causem incidentes.
Implementar um programa de manutenção preventiva eficaz requer planejamento e organização. Aqui estão algumas etapas essenciais para começar:
- Criar um cronograma de manutenção: Defina com que frequência cada máquina deve ser inspecionada e quais procedimentos devem ser realizados durante essas inspeções.
- Treinar a equipe técnica: Certifique-se de que os técnicos estão adequadamente treinados para realizar a manutenção preventiva e sabem identificar sinais de desgaste ou problemas potenciais.
- Documentar todas as atividades de manutenção: Manter registros detalhados das inspeções e reparos realizados ajuda a monitorar a eficiência do programa de manutenção e facilita a identificação de tendências ou problemas recorrentes.
- Utilizar tecnologias avançadas: Ferramentas como sensores de monitoramento e software de gestão de manutenção podem ajudar a identificar problemas antes que eles se tornem críticos, permitindo ações preventivas mais eficazes.
É importante envolver toda a equipe de produção no processo de manutenção preventiva. Operadores e outros trabalhadores que estão em contato direto com as máquinas podem fornecer informações valiosas sobre o desempenho e possíveis problemas que podem não ser aparentes durante inspeções periódicas.
Por fim, lembre-se de que a manutenção preventiva é um investimento, não um custo. Os recursos gastos em inspeções e pequenos reparos são ínfimos em comparação com os custos de consertos emergenciais, perda de produção ou até mesmo a substituição de máquinas inteiras devido a falhas graves. Dessa forma, a implementação de um programa de manutenção preventiva sólido é fundamental para garantir a continuidade da operação e maximizar a eficiência dos equipamentos industriais.
Como Diagnosticar Problemas Comuns em Máquinas Industriais
Diagnosticar problemas em máquinas industriais é uma habilidade crucial para manter a eficiência e produtividade nas montagem industrial empresas. Um diagnóstico preciso pode evitar paradas inesperadas e custos excessivos com reparos. A seguir, abordaremos algumas técnicas essenciais para identificar problemas comuns em máquinas industriais e como enfrentá-los de maneira eficaz.
O primeiro passo no diagnóstico é a observação. Atenção aos sinais visuais e auditivos é fundamental. Vibrações anormais, ruídos altos e sobreaquecimentos são indicadores claros de que algo está errado. Esses sinais podem apontar para problemas em rolamentos, desbalanceamento de componentes e até falhas nos sistemas de lubrificação.
Outra técnica importante é o uso de ferramentas de diagnóstico especializadas. Equipamentos como termovisores, analisadores de vibração e manômetros ajudam a identificar problemas que não são visíveis a olho nu. Por exemplo, um termovisor pode detectar áreas de superaquecimento em motores e componentes elétricos, o que pode indicar falhas iminentes.
Quando se trata de problemas elétricos, a inspeção de painéis e circuitos é essencial. Verificar a integridade dos cabos, conexões e componentes dos Montagem de painéis elétricos industriais pode prevenir falhas catastróficas. Testar os circuitos com multímetros e outros dispositivos de medição elétrica também ajuda a identificar falhas em fusíveis, disjuntores e relés.
Manter registros detalhados de todas as intervenções e problemas detectados é outra prática recomendada. Esses registros ajudam a identificar padrões e frequência de falhas, o que pode apontar para problemas subjacentes mais amplos. Com essas informações, as ações corretivas podem ser mais direcionadas e eficazes.
É crucial também capacitar a equipe envolvida na operação das máquinas. Treinamentos regulares e específicos para o diagnóstico de problemas aumentam a agilidade na identificação de falhas e reduzem o tempo de resposta para correção. Além disso, operadores bem treinados são capazes de identificar sinais de alerta e tomar medidas preventivas antes que os problemas se agravem.
A manutenção preditiva, que usa tecnologia avançada para monitorar o estado das máquinas em tempo real, é outra ferramenta poderosa no diagnóstico de problemas. Equipamentos com sensores integrados podem fornecer dados precisos sobre o desempenho e a condição das máquinas, alertando sobre problemas potenciais antes que eles causem paradas ou danos.
Por exemplo, sensores de vibração permitem monitorar desbalanceamentos e desalinhamentos, enquanto sistemas de análise de óleo podem detectar contaminação ou desgaste excessivo de componentes. Esses dados são então analisados por software especializado, que pode prever falhas com base em algoritmos de aprendizado de máquina e histórico de dados.
Para diagnósticos mais complexos, não hesite em consultar especialistas em montagem industrial empresas. Profissionais experientes têm o conhecimento e ferramentas adequadas para identificar e resolver problemas rapidamente, minimizando o impacto na produção. Eles podem realizar análises mais profundas e oferecer soluções personalizadas para as necessidades específicas da sua operação.
Em conclusão, a identificação precoce e precisa de problemas em máquinas industriais é fundamental para manter a eficiência e evitar paradas inesperadas. A observação atenta, uso de ferramentas de diagnóstico, treinamento adequado da equipe e integração de tecnologias avançadas são estratégias eficazes para alcançar esse objetivo. Ao fazer isso, você garante a operação contínua e eficiente das suas máquinas, reduzindo custos e aumentando a produtividade.
Escolhendo as Ferramentas Certas para o Conserto
Uma das etapas mais críticas no Manutenção hidráulica industrial e em qualquer outro tipo de manutenção é a escolha das ferramentas corretas. Sem os instrumentos adequados, mesmo os técnicos mais experientes podem encontrar dificuldades para realizar reparos de maneira eficiente e segura.
A primeira consideração ao selecionar ferramentas é a especificidade da tarefa. Ferramentas gerais como chaves de fenda, alicates e martelos sempre têm seu lugar, mas para trabalho especializado, instrumentos específicos são essenciais. Por exemplo, chaves dinamométricas são indispensáveis para garantir o aperto correto de parafusos e porcas em sistemas de alta precisão.
Outro aspecto importante é a qualidade das ferramentas. Produtos de marcas reconhecidas e certificadas tendem a oferecer melhor desempenho e durabilidade. Ferramentas de baixa qualidade podem desgastar-se mais rapidamente e até causar danos aos componentes da máquina, aumentando o tempo e o custo do conserto.
Além da qualidade, a segurança é um fator crítico na escolha das ferramentas. Ferramentas isoladas eletricamente são essenciais para trabalhos em componentes elétricos. Da mesma forma, ferramentas à prova de faísca são obrigatórias em ambientes onde há risco de explosões ou incêndios. Equipamentos de segurança pessoal, como óculos, luvas e capacetes, também nunca devem ser negligenciados.
E a tecnologia também desempenha um papel significativo na manutenção moderna. Ferramentas de diagnóstico automatizadas, como analisadores de vibração e termovisores, permitem uma avaliação mais detalhada e precisa do estado das máquinas. Esses dispositivos podem identificar problemas ocultos, orientando os técnicos para intervenções mais acertadas.
Além disso, o software de gestão de manutenção está se tornando cada vez mais comum. Esses programas registram e analisam dados das máquinas em tempo real, ajudando a prever falhas e otimizar a manutenção preventiva. Além disso, podem manter um inventário atualizado das peças e ferramentas disponíveis, garantindo que todas as necessidades para o conserto estejam sempre à mão.
Para manter a organização e a eficiência, é aconselhável criar kits de ferramentas dedicados para diferentes tipos de conserto. Isso facilita o acesso aos instrumentos necessários e evita a perda de tempo procurando por ferramentas específicas. Por exemplo, um kit pode ser reservado exclusivamente para reparos hidráulicos, enquanto outro é dedicado a intervenções elétricas.
Por ser um processo dinâmico, a manutenção pode demandar ferramentas que não estão no kit padrão. Nestes casos, é vital estabelecer parcerias com fornecedores confiáveis que possam fornecer equipamentos de alta qualidade em tempo hábil. A relação de confiança com esses fornecedores pode fazer a diferença em situações de emergência, minimizando o tempo de inatividade das máquinas.
A formação contínua da equipe também é fundamental. Mesmo com as ferramentas mais avançadas, a eficácia do conserto depende do conhecimento e da habilidade dos técnicos. Treinamentos regulares sobre o uso correto das ferramentas e atualizações sobre novas tecnologias e métodos de conserto podem aumentar significativamente a eficiência e reduzir riscos.
Sebno, garantir que todas as ferramentas estejam sempre em bom estado de conservação é crucial. A manutenção regular das ferramentas, como afiar lâminas e verificar calibrações, garante que elas desempenhem suas funções corretamente e por mais tempo. Ferramentas desgastadas ou mal conservadas podem comprometer o conserto e até aumentar o risco de acidentes.
Resumindo, a escolha das ferramentas certas para o conserto de máquinas industriais é um aspecto crucial para a eficiência e a segurança da manutenção. Ao investir em ferramentas de qualidade, organizá-las adequadamente e garantir a formação contínua da equipe, uma empresa pode otimizar seus processos de manutenção e minimizar o tempo de inatividade das suas máquinas.
Quando Chamar um Profissional Especializado
Uma manutenção eficaz das máquinas industriais pode muitas vezes ser gerida internamente, especialmente quando a equipe técnica é bem treinada e dispõe das ferramentas adequadas. No entanto, há momentos em que chamar um profissional especializado torna-se não apenas recomendável, mas essencial. Saber identificar essas situações é crucial para a continuidade da operação e segurança das instalações.
Uma das principais razões para chamar um especialista é a complexidade técnica da tarefa. Embora as equipes internas possam ser proficientes em manutenção de rotina, certas intervenções exigem conhecimentos especializados que vão além das habilidades disponíveis no local. Problemas complexos em Conserto de máquinas industriais muitas vezes requerem uma compreensão profunda de sistemas específicos e acesso a tecnologias avançadas de diagnóstico que apenas profissionais especializados possuem.
Situações de emergência também justificam a contratação de especialistas. Quando uma máquina crucial para a produção falha subitamente, cada minuto conta. Equipes internas podem não ter a experiência ou os recursos necessários para diagnosticar e corrigir o problema rapidamente. Profissionais especializados geralmente têm acesso a peças de reposição e equipamentos de diagnóstico que podem reduzir significativamente o tempo de inatividade.
Falhas em sistemas críticos de segurança são outra razão primordial para chamar um especialista. Máquinas que exibem sinais de riscos de segurança, como vazamentos de substâncias perigosas, curtos-circuitos em painéis elétricos ou falhas em componentes estruturais, devem ser imediatamente avaliadas por técnicos qualificados. Às vezes, os problemas nos sistemas de Montagem de painéis elétricos industriais podem exigir uma ação rápida e específica para evitar acidentes graves.
Outro cenário no qual a presença de um especialista é vital envolve a introdução de novos equipamentos ou tecnologias. A integração de novos sistemas em uma planta existente pode apresentar desafios únicos. Especialistas não apenas ajudam a instalar e configurar novos equipamentos, mas também treinam a equipe local para operá-los e mantê-los de maneira eficaz.
Por fim, um profissional especializado é fundamental quando há necessidade de certificação e conformidade com regulamentações. Muitas indústrias funcionam sob rigorosas normas de segurança e desempenho que exigem validações regulares por entidades certificadoras. Profissionais especializados garantem que as máquinas e processos estejam em conformidade com as normas aplicáveis, evitando multas e garantindo a segurança dos trabalhadores.
Consultas periódicas com especialistas também são benéficas para auditorias preventivas. Mesmo que não haja um problema específico identificado, a inspeção regular por profissionais experientes pode descobrir áreas de melhoria e prevenir falhas antes que elas se tornem críticas. Essas auditorias geralmente resultam em recomendações detalhadas, que ajudam a otimizar a performance das máquinas.
Chamar um especialista em montagem industrial empresas implica um investimento que se paga ao evitar interrupções na produção, aumentar a vida útil das máquinas e garantir a segurança no local de trabalho. Além disso, a colaboração com esses profissionais desenvolve a competência interna, pois a equipe local aprende novas tácticas e procedimentos ao trabalhar junto com especialistas.
A escolha do especialista certo é crucial. Avaliar o histórico e as qualificações do profissional é essencial para garantir que ele possui a experiência e o conhecimento necessários para resolver os problemas específicos que sua operação enfrenta. Recomendações de outras empresas do setor podem ser um bom ponto de partida, além de verificar certificações e qualificações específicas.
Em resumo, enquanto a manutenção de máquinas industriais pode muitas vezes ser gerida internamente, há situações onde a intervenção de um profissional especializado é essencial. Complexidade técnica, emergência, riscos de segurança, introdução de novos equipamentos, necessidade de conformidade e auditorias preventivas são algumas das situações que justificam essa intervenção. Escolher o especialista certo não só resolve problemas imediatos, mas também contribui para a eficiência e segurança a longo prazo da operação.
Após explorar os principais tópicos discutidos ao longo deste artigo, fica claro que o conserto de máquinas industriais desempenha um papel vital na eficiência e continuidade da produção. Desde a importância da manutenção preventiva até a escolha das ferramentas certas e o momento de chamar um profissional especializado, cada aspecto contribui para um funcionamento mais seguro e produtivo das máquinas.
A manutenção preventiva não só prolonga a vida útil dos equipamentos, mas também evita interrupções inesperadas. Diagnosticar problemas comuns rapidamente ajuda a minimizar o tempo de inatividade. O uso das ferramentas adequadas e de qualidade garante que os reparos sejam eficientes e seguros. E, finalmente, saber quando recorrer a profissionais qualificados pode ser a chave para resolver problemas complexos de maneira eficaz.
Estamos aqui para ajudar você a manter sua operação funcionando sem problemas. Convidamos você a aplicar essas práticas em sua rotina de manutenção e compartilhar suas experiências conosco. Se precisar de ajuda adicional, não hesite em enviar uma mensagem; estamos ansiosos para ajudar.
E você, já implementa alguma dessas práticas na manutenção de suas máquinas industriais? Pense nisso e comece a fazer a diferença hoje mesmo!