Plano de Manutenção Preventiva Industrial como Garantia de Eficiência
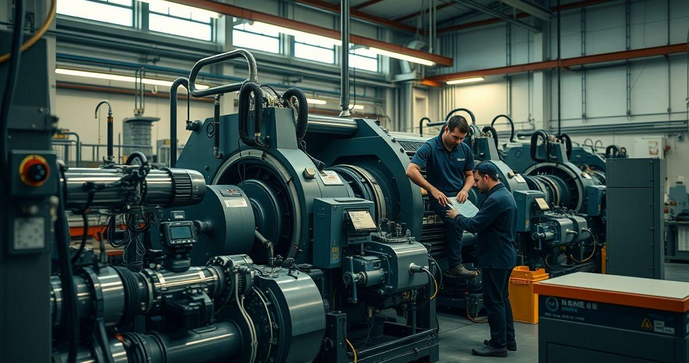
Por: Fabrício - 17 de Abril de 2025
Importância da Manutenção Preventiva na Indústria
A manutenção preventiva desempenha um papel crucial na operação de indústrias de todos os setores. Esse tipo de manutenção se concentra em realizar inspeções e reparos regulares antes que quebras e falhas aconteçam. Isso não apenas garante a operacionalidade contínua dos equipamentos, mas também contribui para a segurança do ambiente de trabalho.
Um dos principais benefícios da manutenção preventiva é a redução significativa de custos com reparos emergenciais. Quando as máquinas são mantidas de forma proativa, as empresas podem evitar as despesas altas associadas a falhas inesperadas, que podem resultar em paradas indesejadas no processo produtivo.
Além disso, a implementação de um plano de manutenção preventiva aumenta a vida útil dos equipamentos. Os ativos industriais geralmente representam um investimento substancial; assim, garantir que funcionem de maneira adequada é essencial para maximizar esse retorno. Com um bom plano, a degradação dos equipamentos é minimizada, resultando em menos substituições e investimentos em novos ativos.
Outro ponto importante a ser considerado é a melhoria na segurança dos trabalhadores. Equipamentos mal conservados podem apresentar riscos significativos, como falhas durante a operação, que podem causar acidentes. A manutenção preventiva ajuda a identificar e corrigir problemas de forma antecipada, promovendo um ambiente de trabalho mais seguro.
Ademais, um plano de manutenção eficaz contribui para a eficiência operacional. Quando os equipamentos são mantidos em bom estado, eles funcionam de maneira mais eficiente, resultando em uma produção mais constante e qualitativa. Isso também pode impactar positivamente a satisfação do cliente, já que atrasos e falhas de qualidade são significativamente reduzidos.
Por último, a manutenção preventiva promove a sustentabilidade das operações industriais. Um uso mais eficiente dos recursos não apenas reduz o desperdício, mas também minimiza o impacto ambiental. Equipamentos que operam em condições ideais consomem menos energia e têm um desempenho ambientalmente mais responsável.
Etapas para a Criação de um Plano de Manutenção Preventiva
Desenvolver um plano de manutenção preventiva eficaz envolve uma série de etapas que garantem a implementação bem-sucedida e a maximização dos benefícios.
A primeira etapa é a realização de um inventário dos equipamentos. Isso inclui a catalogação de todas as máquinas e ferramentas utilizadas na indústria, bem como a coleta de informações cruciais sobre cada uma delas, como uso, idade e histórico de manutenção.
Em seguida, é essencial conduzir uma análise de risco. Identificar quais equipamentos são mais críticos para a operação e quais são os riscos associados a falhas em cada um deles ajuda a priorizar os esforços de manutenção. Classificar a criticidade dos equipamentos também permite direcionar recursos de maneira mais eficiente.
Após a análise de risco, a terceira etapa consiste na definição das atividades de manutenção. Para cada equipamento, é importante especificar quais ações preventivas devem ser realizadas, como inspeções, limpeza, lubrificação e substituição de peças. Além disso, determinar com que frequência essas atividades devem ser executadas é crucial para o sucesso do plano.
Uma vez que as atividades estão definidas, a próxima etapa é o desenvolvimento de um cronograma de manutenção. Esse cronograma deve incluir datas específicas para as atividades, garantindo que todos os responsáveis estejam cientes dos prazos e das tarefas a serem realizadas. Isso ajuda a evitar conflitos de agenda e garante que a manutenção ocorra regularmente.
Além disso, é fundamental garantir que a equipe esteja capacitada para executar as manutenções previstas. Isso pode incluir a realização de treinamentos ou workshops que abordem procedimentos adequados de manutenção e segurança. Ter profissionais qualificados é essencial para que as atividades sejam realizadas de maneira eficiente e sem riscos.
Por último, é importante implementar um sistema de monitoramento e avaliação do plano de manutenção. Utilizar indicadores de desempenho, como tempo de inatividade e custo de manutenção, permite que a equipe avalie a eficácia do plano e faça ajustes conforme necessário. Isso assegura que o plano permaneça relevante e em sintonia com as necessidades da operação.
Ferramentas e Tecnologias para Auxiliar na Manutenção Preventiva
A utilização de ferramentas e tecnologias apropriadas é fundamental para otimizar a manutenção preventiva na indústria. Entre as principais ferramentas estão os softwares de gestão de manutenção, que permitem o planejamento, controle e monitoramento das atividades de manutenção de forma eficaz. Esses sistemas auxiliam na organização de cronogramas, registro de atividades realizadas e no acompanhamento do histórico de manutenção.
Outro recurso valioso são os sensores e dispositivos IoT (Internet das Coisas). Esses sensores podem monitorar condições em tempo real, como temperatura, vibração e pressão, fornecendo dados que ajudam a prever falhas antes que elas ocorram. Com essa tecnologia, é possível fazer ajustes rápidos e adequados, aumentando a eficiência e evitando paradas inesperadas.
Além disso, o uso de drones e câmeras térmicas tem se tornado cada vez mais comum na manutenção preventiva. Os drones permitem inspeções visuais de áreas de difícil acesso, como telhados e estruturas elevadas, enquanto as câmeras térmicas ajudam na detecção de problemas elétricos e mecânicos, como superaquecimento, que podem não ser visíveis a olho nu.
Os softwares de análise preditiva também são importantes aliados na manutenção preventiva. Esses sistemas utilizam algoritmos de inteligência artificial para analisar dados coletados dos equipamentos e prever falhas futuras. Através dessa análise, as empresas podem programar ações de manutenção mais precisas, evitando intervenções desnecessárias e otimizando recursos.
Além dos softwares e tecnologias avançadas, ferramentas tradicionais, como chaves de fenda, multímetros e lubrificantes adequados, continuam sendo essenciais para a manutenção preventiva. A utilização dessas ferramentas deve estar alinhada a um cronograma específico, garantindo que as atividades manuais sejam realizadas de forma eficiente e correta.
Por fim, o treinamento contínuo da equipe é um aspecto crucial para maximizar os benefícios das ferramentas e tecnologias empregadas. Investir na capacitação dos colaboradores para que eles conheçam e utilizem corretamente essas tecnologias aumenta a eficácia da manutenção preventiva e contribui para a melhoria das operações industriais.
Como Avaliar a Eficiência do Plano de Manutenção
A avaliação da eficiência de um plano de manutenção é essencial para garantir que as estratégias implementadas estejam realmente contribuindo para a melhoria operacional da indústria. Um dos principais indicadores que pode ser utilizado para essa avaliação é o tempo de inatividade dos equipamentos. Monitorar o tempo em que as máquinas permanecem paradas devido a falhas ou manutenção permite identificar se o plano está reduzindo essa paralisação.
Outra métrica importante é o custo de manutenção. Comparar os custos com manutenção preventiva e corretiva pode revelar a eficácia do plano. Se o custo com manutenções corretivas for alto em comparação com os investimentos feitos em manutenções preventivas, pode ser um sinal de que ajustes são necessários no plano.
Além disso, a análise do índice de falhas pode fornecer uma visão clara sobre a eficiência do plano. Acompanhando a quantidade de falhas ocorridas ao longo do tempo, a empresa pode observar se há uma redução nos incidentes após a implementação do plano de manutenção preventiva. Uma diminuição nas falhas indica que as estratégias estão funcionando corretamente.
O cumprimento do cronograma de manutenção também serve como um indicador de eficiência. Verificar se as atividades de manutenção estão sendo realizadas conforme planejado ajuda a garantir que todos os procedimentos estão sendo seguidos. A conformidade com o cronograma é um sinal de que a equipe está comprometida e que as práticas de manutenção estão enraizadas na cultura organizacional.
A satisfação dos colaboradores e operários que lidam diretamente com os equipamentos também deve ser considerada na avaliação. Realizar pesquisas e entrevistas pode evidenciar se a equipe percebe melhorias significativas nas condições de trabalho e na eficiência dos equipamentos após a implementação do plano de manutenção.
Por fim, realizar auditorias periódicas e reuniões de revisão do plano de manutenção permite um feedback contínuo sobre sua eficácia. Essas reuniões podem incluir discussões sobre o que está funcionando, o que pode ser melhorado e quais são as prioridades futuras. A atualização constante do plano, com base em dados e feedback, assegura que o processo de manutenção se mantenha relevante e eficaz.
Desafios Comuns na Implementação da Manutenção Preventiva
A implementação de um plano de manutenção preventiva pode enfrentar diversos desafios que, se não forem tratados, podem comprometer sua eficácia. Um dos principais obstáculos é a resistência cultural dentro da organização. Funcionários e até mesmo gerentes podem estar acostumados com práticas reativas, onde a manutenção é realizada apenas após uma falha. Essa resistência ao novo modelo proativo pode dificultar a aceitação da estratégia de manutenção preventiva.
Outro desafio comum é a falta de recursos. Muitas vezes, a implementação de um plano de manutenção preventiva exige investimentos em tecnologias, softwares e capacitação de pessoal, o que pode ser visto como um ônus por parte da gestão. Sem o suporte adequado em termos de orçamento e recursos humanos, o plano pode não ser executado de maneira eficiente, resultando em resultados insatisfatórios.
A escassez de dados históricos sobre falhas e manutenções também pode prejudicar a eficácia do plano. Sem informações adequadas sobre o desempenho dos equipamentos e histórico de falhas, é difícil realizar uma análise precisa e desenvolver um plano de manutenção que aborde as necessidades específicas. Isso pode levar a uma alocação inadequada de esforços e recursos.
Além disso, a falta de treinamento apropriado pode ser um impedimento significativo. É essencial que a equipe que executa o plano de manutenção preventiva tenha o conhecimento e as habilidades necessárias. Sem treinamento adequado, os profissionais podem não seguir as melhores práticas, resultando em desempenhos abaixo do esperado e possíveis falhas não detectadas.
Outro fator a ser considerado são as limitações tecnológicas. Em algumas indústrias, os equipamentos podem ser obsoletos ou não estarem equipados com tecnologias que facilitam o monitoramento e a análise preditiva. Isso pode dificultar a implementação de um plano de manutenção preventiva e levar a estratégias que não contemplam as inovações atuais.
Por último, a integração de sistemas de informação também pode ser um desafio. Muitas organizações podem ter vários sistemas independentes que não se comunicam entre si, dificultando a consolidação de dados necessários para a manutenção preventiva. Essa falta de integração pode prejudicar a análise de desempenho e o acompanhamento eficiente das atividades de manutenção.
Casos de Sucesso de Manutenção Preventiva em Indústrias
Os casos de sucesso em manutenção preventiva demonstram como essa estratégia pode transformar a operação de uma indústria. Um exemplo significativo é de uma fábrica de automóveis que implementou um plano abrangente de manutenção preventiva. Através da análise de dados históricos de falhas e da utilização de sensores de monitoramento em tempo real, a empresa conseguiu reduzir o tempo de inatividade das máquinas em 30% ao longo de um ano. Isso resultou em um aumento significativo na produção e na satisfação do cliente.
Outro caso notável é de uma planta de processamento de alimentos que adotou práticas de manutenção preventiva para aumentar a segurança e a eficiência. Ao implementar inspeções regulares e manutenção programada nos equipamentos de refrigeração, a empresa foi capaz de evitar falhas críticas que anteriormente resultavam em perdas financeiras substanciais devido a produtos estragados. O custo da manutenção preventiva foi rapidamente recuperado através da redução de desperdícios e do aumento da confiabilidade do sistema.
Uma indústria química também obteve sucesso admirável ao integrar um sistema de manutenção preditiva com IoT. Sensores instalados em equipamentos críticos permitiram que a equipe identificasse padrões de desgaste e previsse falhas antes que elas ocorressem. Como resultado, a empresa não apenas reduziu os custos de manutenção corretiva, mas também melhorou a segurança no local de trabalho, diminuindo o número de acidentes relacionados a falhas de equipamento.
Além disso, uma empresa de energia renovável que utiliza turbinas eólicas implementou um plano de manutenção preventiva que incorporava técnicas de análise preditiva. Ao monitorar o desempenho das turbinas em tempo real, a empresa conseguiu detectar falhas iminentes e realizar intervenções antes que se tornassem problemas significativos. Isso levou a um aumento de 25% na eficiência operativa, além de uma economia considerável em custos de reparo.
Em outra indústria, uma empresa de manufatura eletrônica adotou um software de gestão de manutenção que possibilitou o rastreamento das atividades realizadas e a análise dos resultados. Com base nas informações coletadas, foi possível ajustar o cronograma de manutenção, resultando numa redução de 40% nas interrupções não programadas. A colaboração entre a equipe de manutenção e produção também foi fortalecida, melhorando a comunicação e a eficiência.
Esses exemplos demonstram que a aplicação de manutenção preventiva não apenas melhora a eficiência e segurança nas operações, mas também resulta em benefícios financeiros tangíveis. As indústrias que implementam esses planos de forma eficaz colhem os frutos de uma operação mais confiável e lucrativa, promovendo uma cultura de melhoria contínua.
Em resumo, a implementação de um plano de manutenção preventiva é essencial para qualquer indústria que busca otimizar suas operações e garantir a eficiência dos equipamentos. Através da análise dos fatores discutidos, como a importância, etapas para a elaboração, ferramentas necessárias, desafios enfrentados e casos de sucesso, fica claro que essa abordagem não apenas minimiza custos e riscos, mas também aumenta a segurança e a satisfação do cliente.
Além disso, a manutenção preventiva promove uma cultura organizacional voltada para a proatividade e a melhoria contínua. O investimento em tecnologias e capacitação da equipe é fundamental para o sucesso do plano, permitindo que as indústrias mantenham a competitividade em um mercado em constante evolução.
Portanto, ao adotar estratégias de manutenção preventiva, as empresas podem não apenas prolongar a vida útil de seus ativos, mas também garantir um ambiente de trabalho mais seguro e eficiente, contribuindo para o crescimento sustentável do negócio a longo prazo.